Coarse Aggregate Test: Field vs. Lab – Coarse aggregate testing is essential for ensuring construction quality. This guide explores the differences between field and laboratory testing methods for coarse aggregates, based on Indian Standard (IS) codes. Discover which testing approach suits your construction needs best.
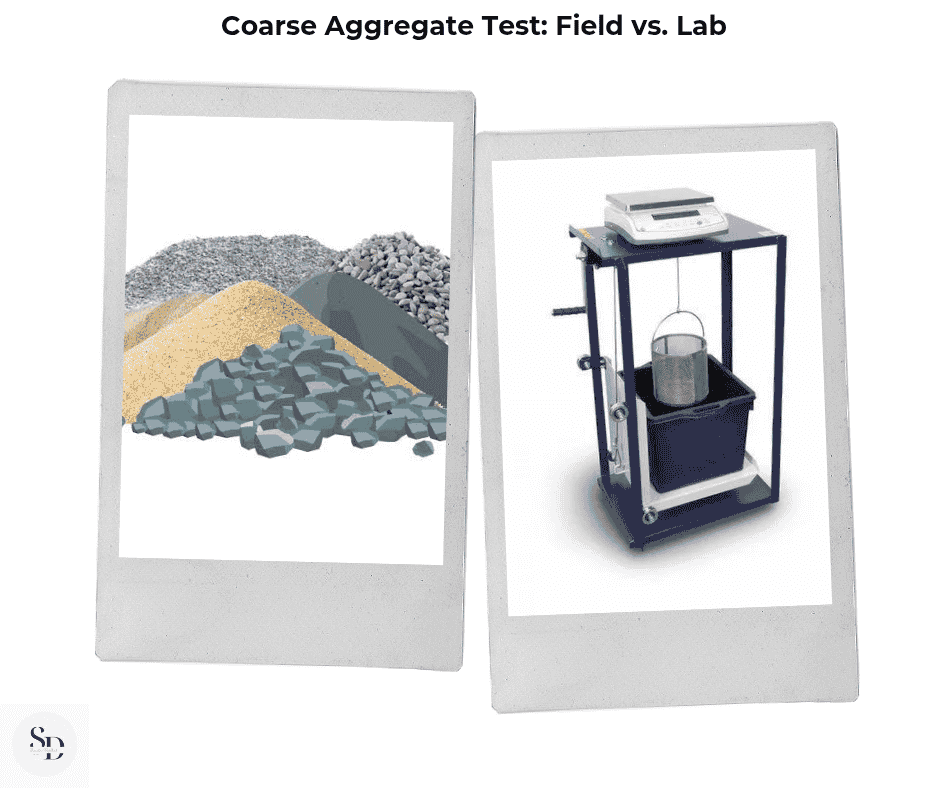
Table of Contents
Introduction
Coarse aggregate forms a fundamental component in construction materials. As the primary ingredient in concrete, it provides essential strength and longevity. But how can we verify if the aggregates meet quality standards? Testing is the answer.
Coarse aggregate testing falls into two main categories:
- Field Tests – Quick assessments performed on construction sites.
- Lab Tests – Comprehensive evaluations conducted in controlled laboratory settings.
Field testing offers rapid results and helps identify obvious flaws, contaminants, and dimensional irregularities. However, these tests may lack precision. This makes laboratory testing essential. Laboratory analysis delivers exact measurements of crucial properties like strength, durability, particle geometry, and moisture absorption. These tests strictly follow Indian Standard (IS) code specifications.
This guide compares field and laboratory testing methods for coarse aggregates. We’ll explore their procedures, significance, and distinctive features. This information will guide you in selecting appropriate testing methods and ensuring aggregate quality.
Basic Details of Coarse Aggregate
What is Coarse Aggregate?
Coarse aggregate refers to natural or crushed stone material used in construction, especially in concrete, roadwork, and railway ballast. According to IS standards, it includes particles exceeding 4.75 mm. These aggregates contribute to concrete’s structural integrity and longevity by forming its core framework.
IS Codes for Coarse Aggregate
Several Indian Standard codes govern coarse aggregate testing and quality standards:
- IS 383:2016 – Aggregate specifications
- IS 2386 (Part 1 to 8):1963 – Aggregate testing methodologies
- IS 456:2000 – Concrete guidelines
Uses of Coarse Aggregate
Key applications include:
- Concrete Production – Enhances structural integrity
- Road Construction – Essential for both bituminous and concrete pavements
- Railway Ballast – Ensures track stability and drainage
- Drainage Systems – Critical for foundation and filtration
- Base Material for Buildings – Provides construction project foundations
Density of Coarse Aggregate
Coarse aggregate density varies based on size, shape, and compaction level:
- Loose Bulk Density – 1200 to 1750 kg/m³
- Compacted Bulk Density – 1400 to 1800 kg/m³
Specific Gravity of Coarse Aggregate
The specific gravity of coarse aggregate typically ranges from 2.5 to 3.0, varying according to the rock type from which it originates. Testing follows the guidelines outlined in IS 2386 (Part 3):1963.
Types of Coarse Aggregate
Coarse aggregates are categorized into different groups based on their origin, physical form, and dimensions:
- Based on Source:
- Natural Aggregates – Obtained from natural deposits like riverbeds, gravel pits, and quarries (including river gravel and crushed stones).
- Artificial Aggregates – Manufactured materials such as crushed bricks, slag aggregates, and processed recycled concrete.
- Based on Shape:
- Rounded Aggregates – Natural materials with smooth surfaces, typically found in rivers.
- Angular Aggregates – Mechanically crushed stones featuring sharp edges, providing superior concrete bonding.
- Flaky Aggregates – Materials with thin, flat characteristics that might compromise concrete strength.
- Elongated Aggregates – Extended particles generally unsuitable for construction purposes.
- Based on Size:
- Fine Aggregates – Particles smaller than 4.75 mm, such as sand.
- Coarse Aggregates – Materials larger than 4.75 mm, commonly available in 10 mm, 20 mm, and 40 mm sizes for concrete applications.
Properties of Coarse Aggregate
Coarse aggregates significantly influence construction outcomes, impacting concrete’s strength, longevity, and overall performance. Key properties include:
1. Strength
- Definition: The ability of aggregate to withstand crushing loads.
- Purpose: Determines the compressive strength of concrete.
- IS Code: IS 2386 (Part 4):1963 (Crushing Value Test).
- Ideal Range: Crushing value ≤ 30% for concrete roads and ≤ 45% for other construction.
2. Durability
- Definition: Resistance of aggregate to weathering, wear, and disintegration.
- Purpose: Ensures long life of concrete in harsh conditions.
- IS Code: IS 2386 (Part 5):1963 (Soundness Test).
- Ideal Range: Aggregates should resist freezing, thawing, and chemical attacks.
3. Water Absorption
- Definition: The amount of water the aggregate can absorb.
- Purpose: Affects the water-cement ratio and workability of concrete.
- IS Code: IS 2386 (Part 3):1963.
- Ideal Range: Should be less than 2% for good quality aggregates.
4. Specific Gravity
- Definition: Ratio of the density of aggregate to the density of water.
- Purpose: Helps in mix design calculations.
- IS Code: IS 2386 (Part 3):1963.
- Ideal Range: 2.5 to 3.0 for most aggregates.
5. Shape and Texture
- Definition: The physical form and surface roughness of the aggregate.
- Purpose: Affects bonding, workability, and void content in concrete.
- IS Code: IS 2386 (Part 1):1963.
- Ideal Types: Angular aggregates provide better interlocking and strength.
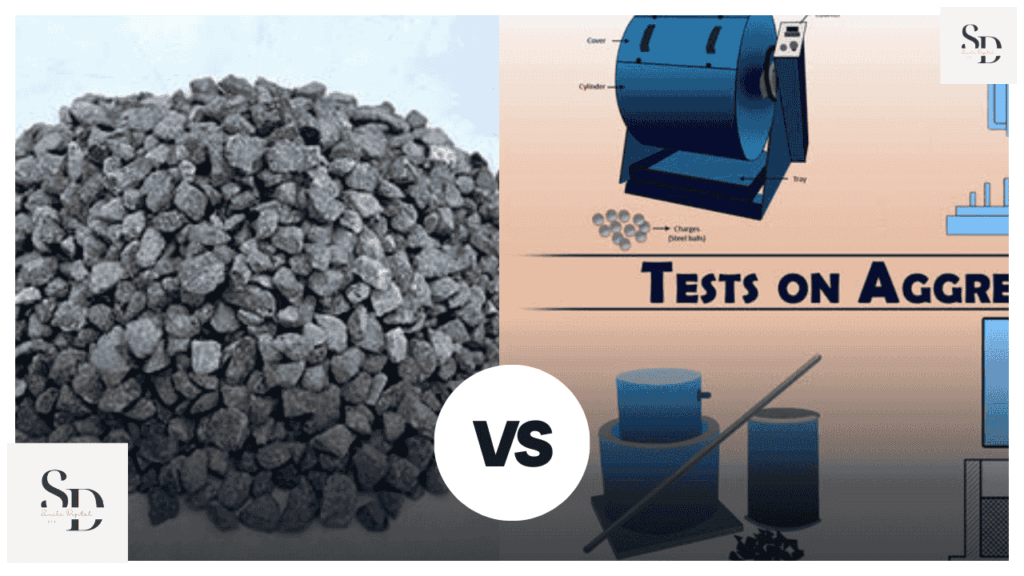
6. Bulk Density
- Definition: Weight of aggregate per unit volume.
- Purpose: Helps in mix proportioning and concrete weight calculations.
- IS Code: IS 2386 (Part 3):1963.
- Ideal Range: 1400 to 1800 kg/m³ (depends on aggregate type).
7. Impact Value
- Definition: Resistance of aggregates to sudden shocks or impacts.
- Purpose: Ensures aggregates can handle dynamic loads like traffic and earthquakes.
- IS Code: IS 2386 (Part 4):1963.
- Ideal Range: ≤ 30% for strong aggregates.
8. Flakiness and Elongation Index
- Definition: Percentage of flaky (thin) and elongated (long) particles.
- Purpose: Ensures aggregates do not weaken the concrete mix.
- IS Code: IS 2386 (Part 1):1963.
- Ideal Range: < 15% for good concrete.
9. Alkali-Silica Reactivity (ASR)
- Definition: The reaction between silica in aggregates and alkali in cement, which can cause cracks.
- Purpose: Prevents expansion and cracking in concrete over time.
- IS Code: IS 2386 (Part 7):1963.
- Ideal Condition: Aggregates should be non-reactive or tested for ASR potential.
10. Fineness Modulus
- Definition: A numerical value representing the particle size distribution of the aggregate.
- Purpose: Helps in selecting the right mix proportions for concrete.
- IS Code: IS 383:2016.
- Ideal Range: 6.0 to 8.0 for coarse aggregates.
Field Tests vs. Lab Tests for Coarse Aggregate
Field Tests:
- Visual Inspection
- Sieve Analysis Test
- Shape and Size Test
- Water Absorption Test
- Surface Moisture Test
- Strength Test (Hand Pressure Test)
- Loose Bulk Density Test
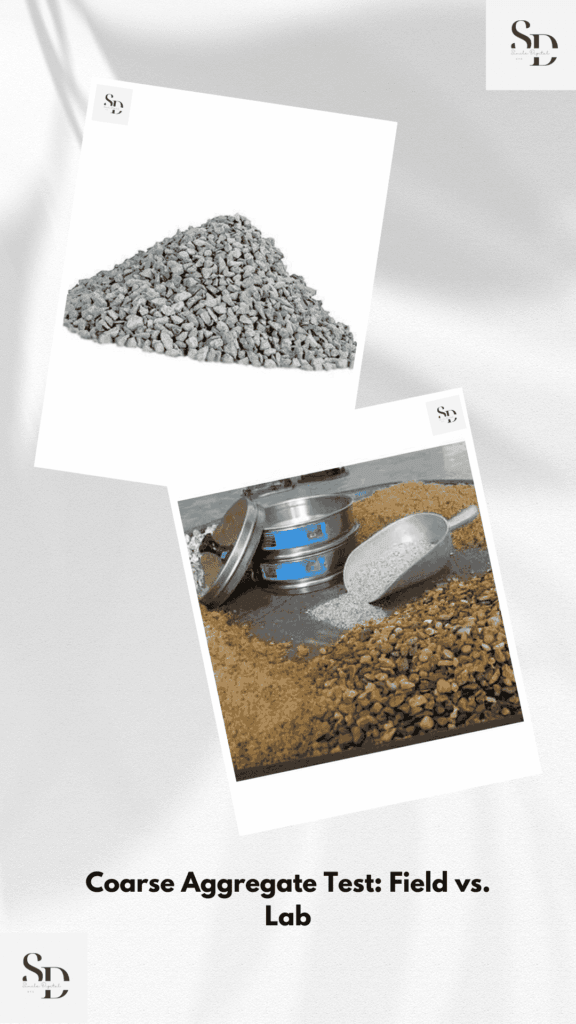
Lab Tests:
- Crushing Value Test
- Impact Value Test
- Abrasion Test (Los Angeles, Deval, or Dorry’s Test)
- Specific Gravity Test
- Water Absorption Test
- Flakiness and Elongation Index Test
- Soundness Test
- Alkali-Silica Reactivity Test
- Bulk Density and Voids Test
- Fineness Modulus Test
Field Tests for Coarse Aggregate
Field tests provide quick, on-site quality assessment methods for coarse aggregates before comprehensive laboratory analysis. These preliminary evaluations help identify fundamental aggregate defects during construction.
1. Visual Inspection
Purpose: To check the appearance, color, shape, and cleanliness of the aggregate.
Procedure:
- Examine the aggregate visually.
- Ensure there are no organic impurities, clay lumps, or excessive dust.
- Good quality aggregates should be hard, durable, and free from cracks.
2. Sieve Analysis Test
Purpose: Evaluates aggregate size distribution through sieve analysis.
Procedure:
- Utilize standardized sieve set (80 mm, 40 mm, 20 mm, 10 mm, 4.75 mm)
- Process aggregate sample through sequential sieve arrangement
- Calculate retention percentages per sieve to verify proper gradation
3. Shape and Size Test
Purpose: Validates aggregate dimensional characteristics and morphology for construction suitability.
Procedure:
- Examine aggregate sample manually to assess shape characteristics
- Identify angular, cubical, or flaky particle geometries
- Note that angular particles enhance structural strength while rounded ones improve workability
- Exclude extensively flaky or elongated particles due to concrete strength reduction risks
4. Water Absorption Test
Purpose: Measures aggregate water absorption capacity, which influences water-cement ratio calculations.
Procedure:
- Select representative dry aggregate sample
- Submerge sample in water for 24-hour duration
- Surface-dry the saturated sample carefully
- Determine weight difference between dry and saturated states
- Consider 2% absorption threshold for concrete mix suitability
5. Surface Moisture Test
Purpose: Assesses aggregate moisture condition to optimize concrete mix proportions.
Procedure:
- Compress handful of aggregate manually
- Check for surface water emergence indicating excess moisture
- Note dull coloration suggesting internal moisture presence
- Modify concrete mix water content accordingly
6. Strength Test (Hand Pressure Test)
Purpose: Evaluates aggregate hardness characteristics.
Procedure:
- Select individual aggregate piece
- Apply pressure using hammer or manual force
- Assess breakage resistance
- Verify adequate strength for construction applications
7. Loose Bulk Density Test
Purpose: Determines aggregate mass per volume unit.
Procedure:
- Fill calibrated container with uncompacted aggregate
- Record filled container mass
- Calculate density using weight-to-volume ratio
- Verify compliance with standard range (1400–1800 kg/m³)
Lab Tests for Coarse Aggregate
Laboratory testing protocols evaluate comprehensive physical, mechanical, and chemical aggregate properties. Following section details essential tests, purposes, relevant IS codes, required equipment, and methodologies.
1. Crushing Value Test
Purpose: Evaluates aggregate compression resistance capabilities.
IS Code: IS 2386 (Part 4):1963
Required Equipment:
- Crushing value testing apparatus with cylindrical steel mold
- Compression testing equipment
- Precision weighing system
- Standard IS Sieves (12.5mm, 10mm, 2.36mm)
Procedure:
- Select aggregates within 10mm-12.5mm size range
- Fill cylindrical mold using three-layer technique with proper tamping
- Apply progressive compressive force using testing apparatus
- Calculate the percentage of crushed material passing through the 2.36mm sieve after compression.
- Standard Limit: Must not exceed 30% for concrete road applications and 45% for other structural uses.
2. Impact Value Test
Purpose: Evaluates aggregate durability under sudden impact conditions.
IS Code: IS 2386 (Part 4):1963
Required Equipment:
- Impact testing apparatus
- Standardized cylindrical metal container
- Compaction rod
- IS Sieves (12.5mm, 10mm, 2.36mm)
- High-precision weighing device
Procedure:
- Select aggregates sized between 10mm to 12.5mm
- Fill testing mold in three distinct layers with proper tamping
- Position sample in impact apparatus and release hammer from 380mm height
- Apply 15 consecutive blows and sieve processed material
- Determine percentage passing through 2.36mm sieve
- Standard Limit: Should not exceed 30% for high-strength aggregates
3. Abrasion Test (Los Angeles, Deval, or Dorry’s Method)
Purpose: Assesses aggregate resistance to wear from friction and abrasion.
IS Code: IS 2386 (Part 4):1963
Required Equipment:
- Los Angeles testing machine with rotating drum and steel spheres
- Precision weighing system
- IS Sieves (20mm, 12.5mm, 1.7mm)
Procedure:
- Introduce 5kg aggregate sample into testing apparatus
- Add appropriate quantity of steel spheres based on aggregate grade
- Rotate drum between 500-1000 cycles
- Screen material through 1.7mm sieve and measure retained portion
- Standard Limit: Maximum 30% for concrete roads, 50% for other applications
4. Specific Gravity Analysis
Purpose: Determines aggregate density and void characteristics.
IS Code: IS 2386 (Part 3):1963
Required Equipment:
- Pycnometer apparatus
- Precision scale
- Temperature-controlled water bath
- Drying oven
Procedure:
- Measure dry aggregate sample weight (W1)
- Record empty pycnometer mass with water (W2)
- Combine aggregate with pycnometer and weigh (W3)
- Calculate Specific Gravity using formula: (W1)/(W3-W2)
- Acceptable Range: 2.6-2.9 for coarse aggregates
5. Water Absorption Analysis
Purpose: Measures aggregate porosity and water retention capacity.
IS Code: IS 2386 (Part 3):1963
Required Equipment:
- Precision weighing device
- Water containment vessel
- Drying oven
Procedure:
- Record initial dry aggregate mass (W1)
- Immerse the aggregate sample completely in water and let it soak for a full 24-hour period.
- After soaking, remove the sample and carefully dry its surface using a clean, absorbent cloth to remove excess moisture.
- Measure and record the weight of the wet aggregate sample (W2).
- Calculate the Water Absorption percentage using the formula: [\frac{(W2 – W1)}{W1} \times 100].
- Quality Standard: For high-grade aggregates, the water absorption value should not exceed 2%.
6. Flakiness and Elongation Index Test
Purpose: Evaluates aggregate particle geometry to ensure optimal shape characteristics.
IS Code: IS 2386 (Part 1):1963
Required Equipment:
- Standardized flakiness gauge
- Calibrated elongation gauge
- IS Sieves (ranging from 63mm to 6.3mm)
- High-precision weighing apparatus
Testing Protocol:
- Screen aggregates through the flakiness gauge to identify and separate thin particles.
- Utilize the elongation gauge to identify and separate particles exceeding length parameters.
- Determine the mass of both flaky and elongated particles independently.
- Quality Standard: Index value should not exceed 15% for structural concrete applications.
7. Soundness Test
Purpose: Evaluates aggregate durability under weathering conditions.
IS Code: IS 2386 (Part 5):1963
Required Equipment:
- Sodium sulfate or magnesium sulfate testing solution
- Temperature-controlled drying oven
- Precision weighing device
Testing Protocol:
- Subject aggregates to five cycles of chemical solution immersion.
- After each cycle, dry specimens at 110°C in the oven.
- Calculate total mass reduction after completing all cycles.
- Quality Standards: Maximum allowable loss – 12% for sodium sulfate method, 18% for magnesium sulfate method.
8. Alkali-Silica Reactivity Test
Purpose: Identifies potential harmful chemical interactions between aggregates and cement.
IS Code: IS 2386 (Part 7):1963
Required Equipment:
- Specialized chemical solutions
- Precision expansion measurement apparatus
Testing Protocol:
- Create a cement-aggregate composite sample and maintain under controlled conditions.
- Monitor and record sample expansion over specified time intervals.
- Quality Standard: Maximum acceptable expansion limited to 0.1% for safe usage.
9. Bulk Density and Voids Test
Purpose: Determines aggregate mass per unit volume and void content.
IS Code: IS 2386 (Part 3):1963
Required Equipment:
- Standard cylindrical measuring container
- Calibrated weighing apparatus
- Standardized tamping rod
Testing Protocol:
- Fill the cylindrical container with aggregate material.
- Calculate bulk density by dividing mass by volume.
- Compare results with standard range (1400–1800 kg/m³).
Best Aggregate for Environmental Sustainability
For sustainable construction practices, optimal choices include Recycled Aggregates, Manufactured Aggregates, and Natural Sustainable Aggregates. These selections support resource conservation, reduce carbon emissions, and promote environmentally responsible construction methods.
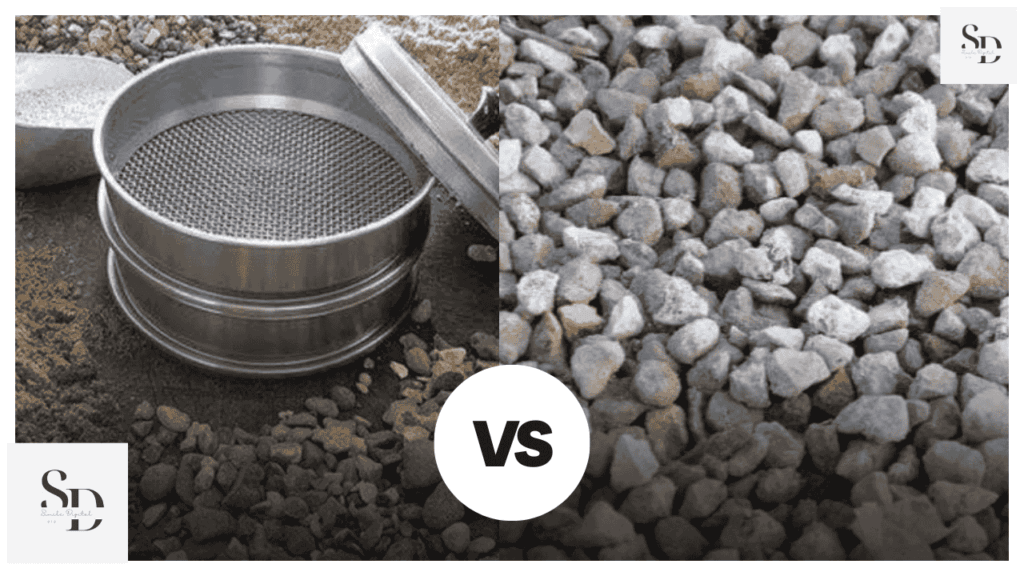
1.Recycled Aggregates (RA)
These are created through the crushing and processing of construction debris, including old concrete structures, used bricks, and demolition materials. This recycling approach significantly minimizes landfill usage, helps preserve natural resources, and reduces carbon emissions from transportation.
How to Use:
- Serves as an effective substitute for natural aggregates in non-load-bearing concrete applications, pavement construction, and road base layers.
- Incorporated in green building projects to achieve sustainability certifications and environmental ratings.
- Particularly effective for low-rise construction projects and various filling applications.
Types:
- Recycled Concrete Aggregate (RCA) – Derived from demolished concrete structures and processed for reuse.
- Recycled Asphalt Aggregate (RAA) – Specifically processed for road construction applications.
- Recycled Brick Aggregate (RBA) – Generated from crushed bricks and ceramic tile waste.
These aggregates are engineered from industrial byproducts and waste materials, offering an environmentally conscious alternative to traditional natural aggregates.
2.Manufactured Aggregates (MA) / Artificial Aggregates
These are produced from industrial waste or by-products, making them a sustainable alternative to natural aggregates.
How to Use:
- Suitable for high-performance concrete applications, lightweight structural elements, and precast components.
- Minimizes the environmental impact of natural stone extraction.
- Provides superior thermal and acoustic insulation properties.
Types:
- Fly Ash Aggregates – Produced from thermal power plant waste materials.
- Slag Aggregates – Created from steel industry blast furnace byproducts.
- Expanded Clay Aggregates – Engineered lightweight materials for sustainable construction.
These materials are sourced through environmentally responsible practices designed to minimize ecological impact.
3.Natural Sustainable Aggregates
These aggregates are obtained ethically and sustainably to minimize environmental harm.
How to Use:
- Implemented in permeable pavement systems to enhance groundwater replenishment.
- Sourced exclusively from certified sustainable quarrying operations.
- Applied in pervious concrete applications for environmentally conscious infrastructure.
Types:
- Crushed Stone Aggregates – Obtained through responsible quarrying practices.
- River Pebbles – Utilized in sustainable landscaping and flooring solutions.
- Bamboo Charcoal Aggregates – Advanced material for reducing carbon footprint.
How to Promote Sustainable Use of Aggregates?
- Prioritize locally sourced aggregates to minimize transportation emissions.
- Implement comprehensive construction waste recycling programs.
- Incorporate supplementary materials like fly ash and slag as aggregate alternatives.
- Adhere to established green building standards and sustainable construction guidelines.
Books
1. Concrete Technology: Properties and Testing of Aggregates – A.M. Neville
2. The Artificial Coarse Aggregate – K. Subramanya
3. The Aggregates Handbook – National Stone, Sand & Gravel Association
4. Testing Aggregates – George F. Blackledge
Conclusion
Coarse aggregates are fundamental to construction, affecting concrete’s structural integrity and performance characteristics. Quality assurance through standardized testing ensures compliance with IS codes. While field testing provides rapid assessment capabilities, laboratory analysis delivers precise measurements essential for construction applications.
Key selection criteria include crushing strength, impact resistance, water absorption properties, specific gravity, particle shape, and durability factors. The growing adoption of recycled and sustainably sourced aggregates reflects the industry’s environmental consciousness. Optimal aggregate gradation combined with favorable physical properties contributes to durable, environmentally responsible structures.
For environmental sustainability, responsibly sourced crushed stone remains optimal. Recycled aggregate utilization further supports eco-friendly construction practices. River sand extraction should be carefully managed to protect aquatic ecosystems.
By implementing comprehensive testing protocols and strategically selecting appropriate aggregates, construction professionals can develop resilient, long-lasting, and environmentally sustainable infrastructure that serves multiple generations.
Thank You Note
Thank you for exploring this comprehensive guide on Coarse Aggregate Field Test vs. Lab Test. This resource aims to help construction professionals, engineers, and students grasp the critical role of aggregate testing in quality construction. We welcome your questions and insights. Together, let’s create a more resilient and sustainable built environment!
Frequently Asked Questions (FAQs)
What is the ideal specific gravity for coarse aggregate?
What are the key differences between field and lab tests for coarse aggregate?
Why is coarse aggregate important in construction?
What type of coarse aggregate is best for environmentally sustainable construction?
Why should we avoid flaky and elongated aggregates?
How does water absorption affect aggregate quality?
Which IS code is used for testing coarse aggregate quality?
Note for Readers
If you’d like to read this blog in your regional language or any other international language, simply click on the Google Translator option located in the bar at the top of the page. This feature allows you to select your preferred language and enjoy the content in a way that’s comfortable for you. We hope this makes your reading experience more enjoyable and accessible!
Disclaimer
This article is for educational and informational purposes only. While every effort has been made to provide accurate and up-to-date information, always refer to Indian Standard Codes (IS codes) and consult professionals before making construction decisions. The use of materials should be based on local regulations and environmental considerations.
For more exciting topics, explore our other articles here
4 Comments