Steel Test: Field vs Lab – Discover the key differences between field tests and laboratory tests for reinforcement steel used in RCC. Learn how both testing methods work, what they reveal, and why they are essential for quality control in construction.
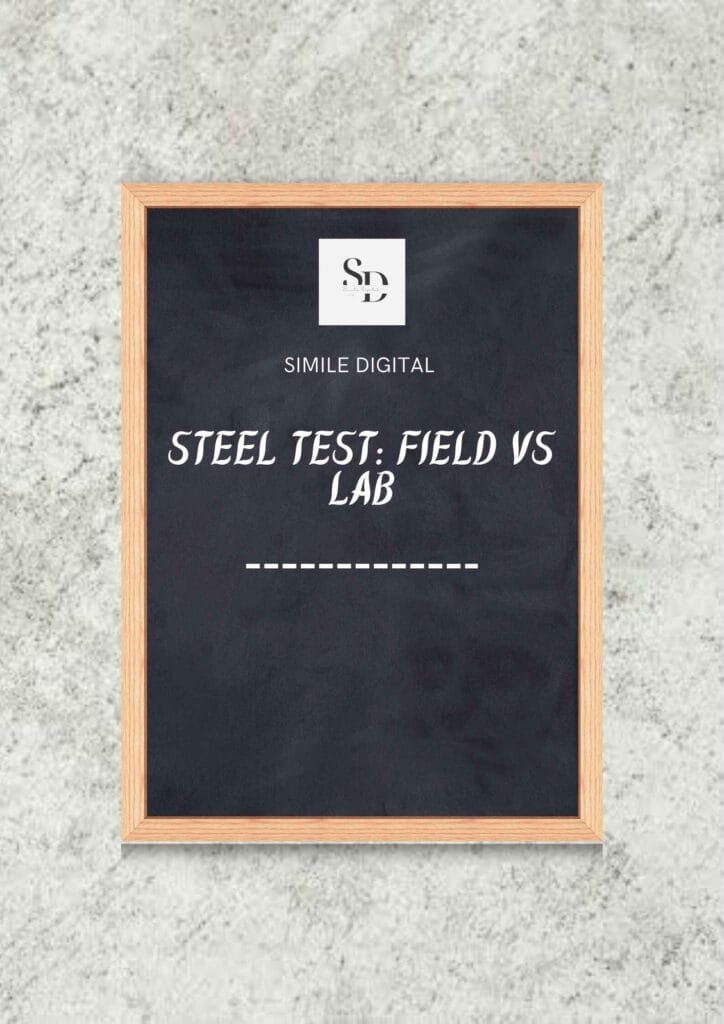
Table of Contents
Introduction
In the world of construction, the strength and durability of a structure depend heavily on the quality of reinforcement steel. But how do engineers ensure that the steel used on-site meets the necessary standards? The answer lies in testing — and there are two main approaches: field testing and laboratory testing.
Field tests are quick, on-the-spot checks that help identify obvious flaws or defects in steel bars. These are essential for day-to-day decision-making on construction sites. On the other hand, laboratory tests offer precise and detailed analysis of the steel’s mechanical and chemical properties. They follow standardized methods and give engineers confidence in the material’s long-term performance.
This blog, titled “Steel Test: Field vs Lab”, dives deep into both methods. We’ll explain how each test is conducted, what parameters they assess, and why combining both approaches ensures safe and strong construction. If you’re an engineer, site supervisor, student, or construction enthusiast — this guide will give you clarity on how steel is tested and trusted before becoming part of our built environment.
What is Reinforcement Steel?
Reinforcement steel, also known as rebar (reinforcing bar), is a high-strength steel used in reinforced cement concrete (RCC) structures to resist tensile, shear, and sometimes compressive forces. While concrete is strong in compression, it is weak in tension — that’s where steel reinforcement comes into play. It bonds well with concrete, expands and contracts similarly with temperature, and helps in distributing loads efficiently.
Grades of Reinforcement Steel (As per IS 1786)
- Fe 415: Yield strength 415 N/mm²
- Fe 500: Yield strength 500 N/mm²
- Fe 500D / Fe 550D: More ductile, used in seismic zones
- Fe 600: Higher strength, used where less steel is desired for the same strength
Properties of Reinforcement Steel
- High Tensile Strength – Can bear large pulling forces.
- High Yield Strength – Begins to deform plastically only under high stress.
- Good Ductility – Can bend or stretch before breaking.
- Strong Bond with Concrete – Especially in deformed/TMT bars.
- Thermal Compatibility – Expands/contracts similarly with concrete.
- Corrosion Resistance – Especially in TMT and epoxy-coated bars.
- Weldability – Most modern bars can be welded with ease.
- Modulus of Elasticity – 2 × 10⁵ N/mm² (or 200 GPa).
- Density – 7850 kg/m³
- Specific Gravity – 7.85
IS Codes Related to Reinforcement Steel
- IS 1786:2008 – High Strength Deformed Steel Bars and Wires for Concrete Reinforcement.
- IS 432 Part 1:1982 – Mild Steel and Medium Tensile Steel Bars.
- IS 1608:2005 – Tensile Testing of Metals.
- IS 456:2000 – Code of Practice for Plain and Reinforced Concrete.
- IS 13920:2016 – Ductile Detailing of Reinforced Concrete Structures (important for seismic zones).
- IS 2502:1963 – Bending and Fixing of Bars.
How to Calculate Reinforcement Quantity
To calculate reinforcement in an RCC element (beam, slab, column), you generally use the following:
- Bar Weight per Meter Formula:
- Weight (kg/m) = (D² × 1) / 162
- Where D = Diameter of the bar in mm
- Example: For 12 mm bar → (12 × 12)/162 = 0.89 kg/m
2. Total Steel Weight Formula (for quantity):
- Weight (kg) = (D² / 162) × Length (in meters) × Number of Bars
3. Percentage of Steel in RCC Members:
- Slabs: 0.7% to 1% of volume
- Beams: 1% to 2% of volume
- Columns: 1% to 4% of volume
You can use:
Steel (kg) = % of steel × Volume of concrete × 7850
4. Example Calculation
- Let’s say you have 10 bars of 16 mm diameter, each 12 meters long.
- Step 1: Find unit weight of 16 mm bar
= (16 × 16)/162 = 1.58 kg/m - Step 2: Total length = 10 bars × 12 m = 120 m
Total weight = 1.58 × 120 = 189.6 kg
Reinforcement Steel: Chemical Composition, Material Used, and Cost vs Strength
Basic Composition & Materials Used:
- Reinforcement steel, also known as rebar, is primarily made from iron ore or scrap steel through steelmaking processes like basic oxygen or electric arc furnaces. The key chemical elements in reinforcement steel include:
- Carbon (C): 0.2% to 0.3% – Controls strength and ductility.
- Manganese (Mn): 0.5% to 1.5% – Enhances toughness.
- Sulphur (S) and Phosphorus (P): Usually below 0.05% – These are impurities that reduce ductility if present in high amounts.
- Silicon (Si): Around 0.15% to 0.3% – Improves strength and corrosion resistance.
- Copper (Cu), Chromium (Cr), Nickel (Ni): Present in small amounts for corrosion resistance, especially in CRS bars.
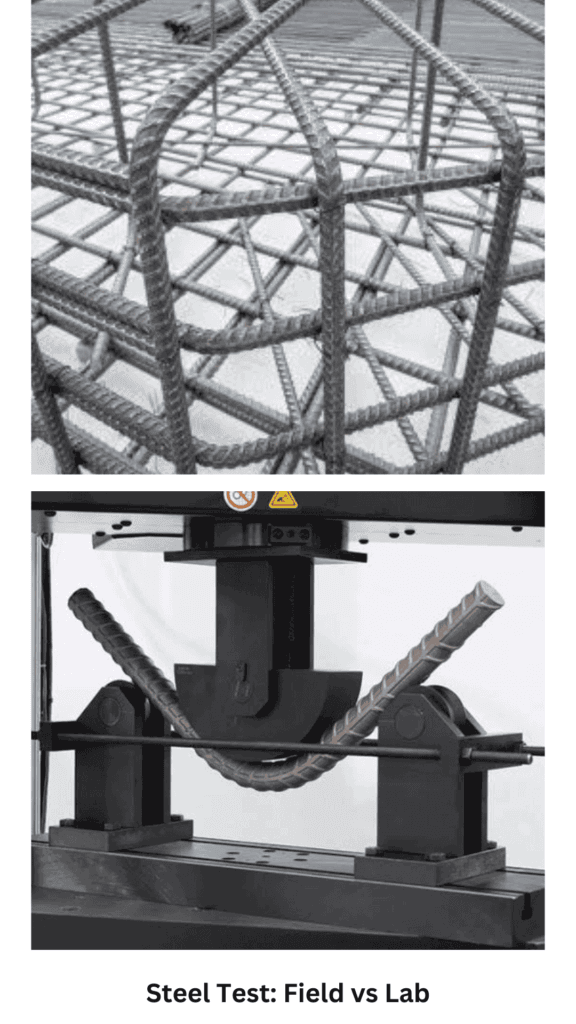
Material Strength and Cost Relation:
- Fe 415: Common in residential buildings. More ductile and economical but requires more quantity of steel.
- Fe 500: Most widely used today. Offers better strength with less quantity needed, slightly higher cost than Fe 415.
- Fe 500D or Fe 550D: Better ductility for seismic zones or high-load structures. Costlier but offers safety in design.
- Fe 600: Used in high-rise buildings and heavy infrastructure where high strength is a priority.
- As strength increases, cost per ton also increases, but total quantity required reduces — so overall project cost can sometimes balance out.
Types of Reinforcement Steel (Used in RCC Construction)
a) Mild Steel Bars (MS Bars):
- Yield strength around 250 N/mm².
- Smooth surface.
- Rarely used now due to lack of bonding and low strength.
b) High Yield Strength Deformed Bars (HYSD Bars):
- Introduced after MS bars.
- Deformed (ribbed) surface for better bonding.
- Grades: Fe 415, Fe 500, etc.
c) Thermo Mechanically Treated Bars (TMT Bars):
- Most commonly used today.
- Outer surface hard, core soft — gives strength + flexibility.
- Available in Fe 415, Fe 500, Fe 500D, Fe 550, Fe 600.
d) Corrosion Resistant Steel (CRS Bars):
- Special chemical treatment for coastal or saline environments.
- More expensive but prevents corrosion damage.
e) Epoxy-Coated or Galvanized Rebars:
- Extra protection layer.
- Used in bridges, marine structures, etc.
Standard Market Sizes & Bar Lengths in India
Bar Diameters Commonly Available:
- 6 mm – used for stirrups and light structures.
- 8 mm – secondary reinforcement, distribution bars, slab.
- 10 mm – light structural members.
- 12 mm – beams, columns.
- 16 mm – major structural elements.
- 20 mm – footings, columns.
- 25 mm – heavy RCC.
- 28 mm, 32 mm – industrial, bridges, flyovers.
- So generally available sizes are: 6mm, 8mm, 10mm, 12mm, 16mm, 20mm, 25mm, 28mm, 32mm.
Standard Bar Lengths:
- 12 meters (Standard Length): Most commonly available.
- Cut Lengths: Available based on project requirement.
- Custom Lengths: Like 6m, 15m, or coils for smaller diameters (6mm–10mm).
Classification of Steel
Steel is generally classified based on its carbon content, manufacturing process, and application:
1. Based on Carbon Content:
- Low Carbon Steel (up to 0.25% carbon) – soft, ductile, used for wire, sheets.
- Medium Carbon Steel (0.25% to 0.6%) – stronger, used for rails, gears.
- High Carbon Steel (0.6% to 1.5%) – very strong, used for tools and springs.
2. Based on Use in Construction:
- Mild Steel Bars (MS)
- HYSD Bars
- TMT Bars
- CRS Bars
- Prestressing Steel (strands or wires)
Manufacturing Process of Steel (Basic Idea)
1. Primary Steel Making:
- Blast Furnace-Basic Oxygen Furnace (BF-BOF): Iron ore + coke + limestone heated → molten iron → impurities removed with oxygen.
- Electric Arc Furnace (EAF): Scrap steel melted with electric arcs → cleaner steel.
2. Secondary Steel Making:
- Refining and alloying for strength, ductility, and corrosion resistance.
3. Casting and Forming:
- Molten steel is cast into billets.
- Rolled into rods or bars using hot rolling mills.
4. Thermo-Mechanical Treatment (for TMT Bars):
- Hot rolled bars rapidly quenched → hard outer layer forms.
- Core cools slowly → remains soft and ductile.
Tests of Steel (Rebar)
Field Tests of Steel
- Visual Inspection
- Bend Test
- Re-bend Test
- Ring Test
- Rust Check Test
- Dimension Check (Length & Diameter)
- Weight per Meter Verification
- Spark Test (occasionally used)
- Magnetic Test (to check consistency)
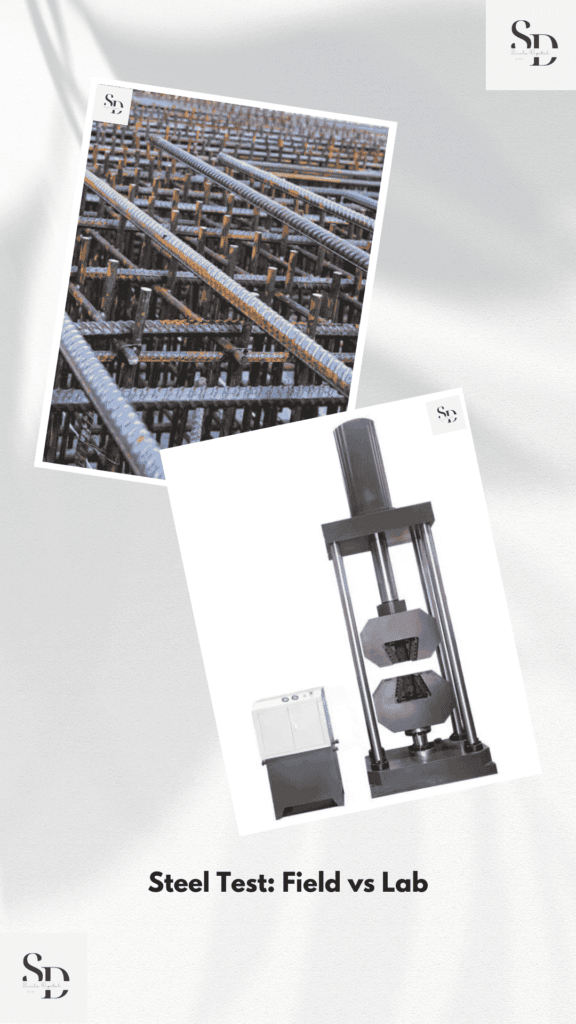
Lab Tests of Steel
- Tensile Strength Test
- Yield Strength Test
- Elongation Test
- Bend and Re-bend Test (Standardized)
- Chemical Composition Test
- Hardness Test
- Fatigue Test
- Impact Test (Charpy Test)
- Modulus of Elasticity Test
- Corrosion Resistance Test
- Weldability Test
Field Tests of Steel
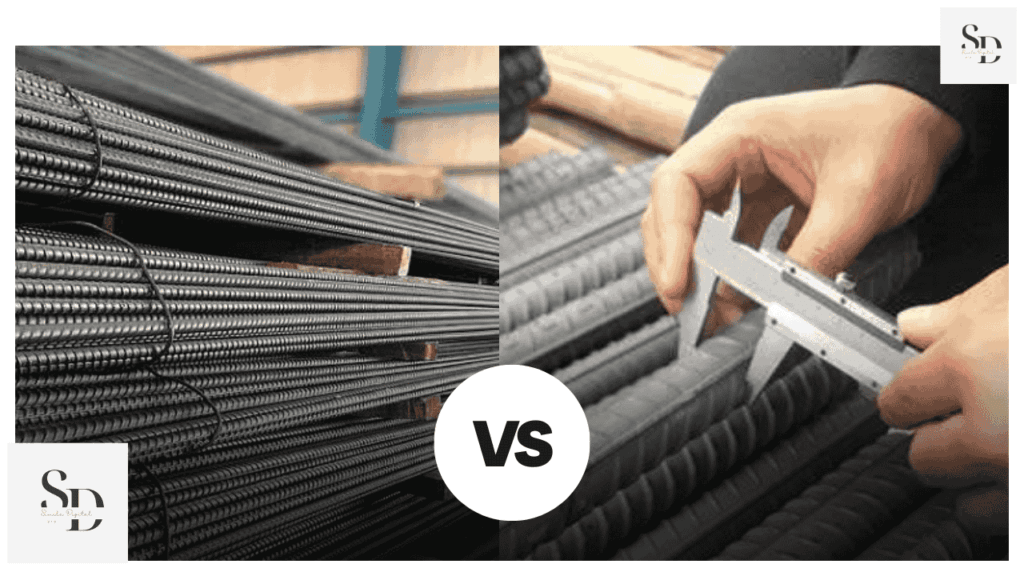
1. Visual Inspection
Objective: To check for visible defects like rust, cracks, bends, flaky surface, or oil/grease coating.
Apparatus Required:
- Measuring tape (optional)
- Torch (for low light)
Procedure:
- Visually examine the full length of the steel bar.
- Check for loose or flaky rust.
- Look for any deep pits, dents, or unusual bends.
- Ensure the surface is free from oil, grease, paint, or mud.
- Confirm there’s no visible damage from storage or transport.
Acceptance Criteria:
- Slight rust (thin film) is acceptable.
- Deep rust, flaky scaling, oil, or dents should be rejected.
2. Bend Test (Field Version)
Objective: To check the ductility and flexibility of steel – whether it cracks or breaks when bent.
Apparatus Required:
- A hammer
- A solid support (like a block or angle)
- Pipe or bending lever (manual bending rod)
Procedure:
- Take a bar of about 600 mm length.
- Place the bar on support and start bending it manually using the pipe or hammer.
- Try bending it to around 135° or more.
- Inspect the bend area.
Acceptance Criteria:
- No cracks or rupture should appear on the outer surface.
- A small hairline surface crack may be tolerable but no deep cracking.
3. Re-bend Test (Field Version)
Objective: To ensure that the bar can withstand re-bending without failure, as happens during construction.
Apparatus Required:
- Same as bend test
- Bucket of hot water (optional, to simulate site conditions)
Procedure:
- First perform a bend test up to 135°.
- Keep the bar in hot water (~100°C) for 30 minutes.
- Then unbend and again re-bend it in the opposite direction up to 157.5°.
- Check for cracks.
Acceptance Criteria:
- The bar should not break or develop major cracks on rebending.
4. Ring Test
Objective: To check the soundness and internal uniformity of steel.
Apparatus Required:
- A steel bar
- A hammer
- Concrete floor or solid surface
Procedure:
- Hold the bar vertically and strike it lightly with a hammer.
- Listen to the sound it produces.
Acceptance Criteria:
- A clear, ringing metallic sound indicates good steel.
- A dull sound may indicate internal cracks or poor quality.
5. Rust Check Test
Objective: To determine whether rust on the bar is harmful or just surface-level.
Apparatus Required:
- Wire brush or cloth
- Magnifying glass (optional)
Procedure:
- Rub the surface with a wire brush.
- If rust comes off easily and bar shines underneath, it’s acceptable.
- If deep pits or scaling remain, the steel is corroded.
Acceptance Criteria:
- Surface rust is okay.
- Deep rust or scaling is not acceptable.
6. Dimension Check (Length & Diameter)
Objective: To verify the diameter and length of bars as per requirement.
Apparatus Required:
- Measuring tape
- Vernier caliper or steel scale
Procedure:
- Measure the bar diameter at two or three different points.
- Measure the full bar length using tape.
- Check rib spacing (optional).
Acceptance Criteria:
- Tolerance of ±0.5 mm is generally accepted.
- Length as per bar bending schedule.
7. Weight per Meter Verification
Objective: To verify the actual weight of the bar and cross-check with theoretical weight.
Apparatus Required:
- Weighing machine
- Measuring tape
- Calculator
Procedure:
- Measure 1 meter of the bar.
- Weigh it on a scale.
- Compare with theoretical weight using formula:
W = (D² × 1)/162
Where D = Diameter in mm
Acceptance Criteria:
- Actual weight should match theoretical within 3–5% tolerance.
8. Spark Test (Optional)
Objective:
To quickly check for the type of steel based on the spark pattern (used rarely on site).
Apparatus Required:
- Grinding wheel
Procedure:
- Touch the steel to a running grinding wheel.
- Observe the spark pattern.
- Bright, consistent sparks indicate carbon steel.
Acceptance Criteria:
- Inconclusive without lab. Mostly indicative only.
9. Magnetic Test (Rarely used)
Objective: To check for any non-ferrous contamination in steel.
Apparatus Required:
- Strong magnet
Procedure:
- Move the magnet over the steel bar.
- If there’s any area that doesn’t attract magnet, it may be impure.
Acceptance Criteria:
- Reinforcement should be fully magnetic.
- Non-magnetic zones may mean impurities or mixing with non-ferrous metals.
Laboratory Tests of Steel
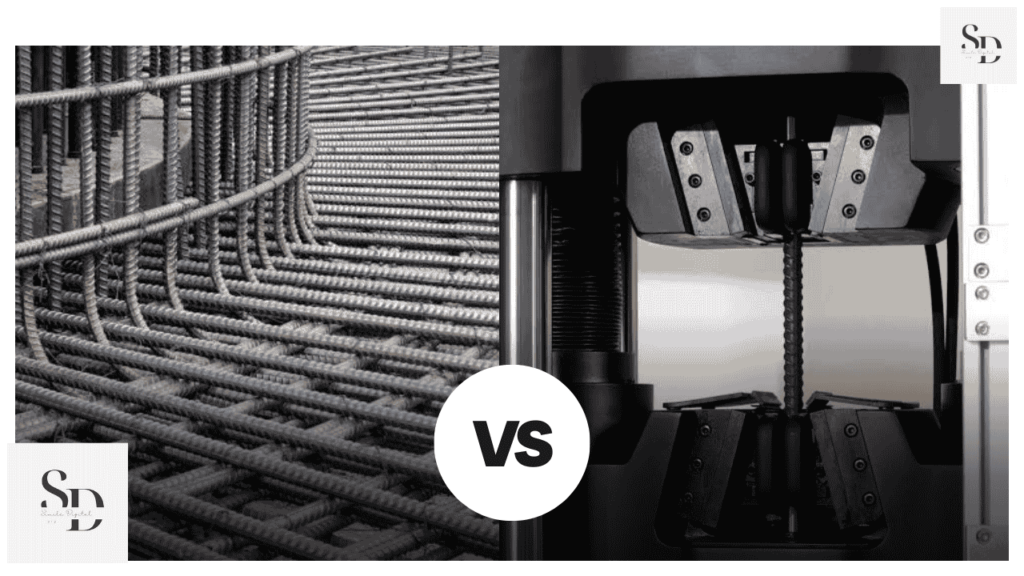
1. Tensile Strength Test
Objective: To determine the tensile strength, yield strength, and elongation of a steel bar – basically how much load the bar can take before it starts stretching and ultimately breaks.
Apparatus Required:
- Universal Testing Machine (UTM)
- Steel specimen (standard length, usually 600 mm or as per IS code)
- Vernier caliper
- Punch or marker for gauge length
Procedure:
1. Select a steel bar as per required grade (e.g., Fe500, Fe415).
2. Cut it to standard length (usually around 600 mm).
3. Mark the gauge length (usually 5 times the diameter or 200 mm, whichever is specified).
4. Fix the bar firmly between the two grips of the UTM.
5. Start the test by applying axial tension load slowly and continuously.
6. Observe and record the load at yield point, ultimate tensile load, and breaking load.
7. Measure the final elongation between gauge marks after breaking.
8. Note all readings – Yield Strength = Load at yield point / Cross-section area,
Ultimate Strength = Max load / Area,
Percentage Elongation = (Final length – Original length) / Original length × 100.
Acceptance Criteria:
As per IS 1786:
- Fe415 steel should have minimum yield strength = 415 N/mm²
- Elongation should not be less than 14.5%
- Results must match the values for the specific grade.
2. Bend and Re-bend Test (Lab Standard)
Objective: To check the ductility and flexibility of the reinforcement bar under controlled lab conditions.
Apparatus Required:
- Mandrel (steel rod or fixture)
- Universal Bend Testing Machine
- Hot water (for re-bend)
- Timer
Procedure:
For Bend Test:
1. Cut a test specimen of 500 mm or as per IS 1599.
2. Place it on the bending machine with a mandrel of size as per IS 1786.
(Mandrel size depends on bar diameter and grade – e.g., 4d, 5d, etc.)
3. Bend the bar smoothly to 180° using the machine.
4. Remove and inspect the bent area.
For Re-bend Test:
5. Heat the bent specimen in hot water (100°C) for 30 minutes.
6. After cooling, re-bend it to 157.5° in the opposite direction.
7. Check for cracks or surface rupture.
Acceptance Criteria:
- No visible cracks or rupture in either bend or re-bend test.
3. Chemical Composition Test
Objective: To determine the percentage of carbon, manganese, sulfur, phosphorus, etc. in the steel.
Apparatus Required:
- Spectrometer (Optical Emission Spectroscopy)
- Sample cutting machine
- Polishing tool
Procedure:
1. Take a small sample from the steel bar.
2. Polish the surface to remove oxide or rust.
3. Place it on the spectrometer table.
4. Start the spectrometer – it uses arc or spark discharge to analyze elements.
5. Results will show the composition of carbon, silicon, manganese, sulfur, phosphorus, chromium, etc.
Acceptance Criteria (IS 1786):
- Carbon ≤ 0.30%
- Sulfur ≤ 0.055%
- Phosphorus ≤ 0.055%
- Carbon Equivalent ≤ 0.42%
4. Hardness Test
Objective: To measure the hardness of steel – how resistant it is to deformation or indentation.
Apparatus Required:
- Brinell Hardness Testing Machine (BHN)
- Steel test sample (flat and smooth)
Procedure:
1. Place the steel specimen on the BHN machine base.
2. Apply a fixed load using a steel ball for 15 seconds.
3. Remove load and measure the diameter of the indentation using microscope or measuring device.
4. Use standard BHN formula to calculate hardness.
Acceptance Criteria:
- Steel bars generally fall between 120–180 BHN depending on grade.
5. Impact Test (Charpy Test)
Objective: To determine the toughness of the steel – its ability to absorb impact energy.
Apparatus Required:
- Charpy Impact Testing Machine
- V-notched steel specimen
- Scale for energy reading
Procedure:
1. Prepare a V-notched specimen (10 × 10 × 55 mm) from steel bar.
2. Place it horizontally with notch facing opposite to striking side.
3. Release the pendulum hammer from a fixed height.
4. Record the energy absorbed during fracture – shown on machine scale.
Acceptance Criteria:
- Value depends on grade and temperature, but higher energy absorbed means tougher steel.
6. Modulus of Elasticity Test
Objective: To determine the stiffness of steel – how much it stretches under a given load.
Apparatus Required:
- Universal Testing Machine
- Extensometer
- Steel specimen
Procedure:
1. Mount extensometer on the test bar.
2. Fix the specimen on UTM.
3. Apply load gradually and record stress vs strain.
4. Plot stress-strain graph – the slope of initial straight portion = Modulus of Elasticity (E).
5. E = Stress / Strain in elastic limit.
Standard Value for Steel:
- Modulus of Elasticity = 2 × 10⁵ N/mm²
7. Fatigue Test
Objective: To check how many load cycles a steel bar can withstand before failure — useful where bars face repeated loading (like in bridges or heavy traffic areas).
Apparatus Required:
- Fatigue Testing Machine
- Steel specimen
- Counter for number of cycles
Procedure:
1. Place the steel specimen in the fatigue testing machine.
2. Apply a repeated cyclic load (can be bending, axial, or torsional) at a specific amplitude and frequency.
3. Continue the test until the specimen breaks or shows signs of fatigue failure.
4. Record the number of cycles to failure.
Acceptance Criteria:
- Higher the number of cycles before failure, better the fatigue resistance.
8. Weldability Test
Objective: To assess whether the steel bar can be easily welded without cracks or affecting strength.
Apparatus Required:
- Welding machine (Arc/MIG)
- Steel bars
- Grinding/polishing tools
- Inspection tools (microscope or magnifier)
Procedure:
1. Prepare two ends of the reinforcement bar and weld them together.
2. Allow to cool at room temperature.
3. Grind and polish the welded area to inspect clearly.
4. Examine visually or under microscope for any cracks or porosity.
5. If needed, bend or tensile test can be performed post-welding.
Acceptance Criteria:
- No surface or internal cracks.
- Welded area must retain at least 90% of the bar strength.
9. Corrosion Resistance Test
Objective: To test how resistant the steel is to rust or corrosion when exposed to moisture or chemicals.
Apparatus Required:
- Salt spray chamber or corrosion bath
- Weighing scale
- Steel specimen
- Timer
Procedure:
1. Clean and weigh the steel bar before testing.
2. Place the bar in a salt spray chamber (usually 5% NaCl solution) or immerse in saline water.
3. Keep it for a specified duration (e.g., 48–72 hours).
4. Remove and clean off any loose rust.
5. Weigh again and calculate the weight loss.
Acceptance Criteria:
- Lower the weight loss, better the corrosion resistance.
- Epoxy-coated or TMT bars generally perform better than plain bars.
10. Yield Strength Test of Reinforcement Steel
Objective: To determine the yield strength of reinforcement steel, which is the stress at which steel starts to deform plastically.
Apparatus Required:
- Universal Testing Machine (UTM) – minimum capacity 1000 kN.
- Steel specimen – typically 8mm, 10mm, 12mm etc., cut to required gauge length.
- Vernier Caliper / Micrometer – for measuring diameter.
- Extensometer (optional) – for measuring strain precisely.
Procedure:
1. Measure the diameter of the test bar at three locations and take the average.
2. Gauge length is marked on the bar (5.65 × √A, where A is cross-sectional area).
3. Place the steel specimen in the jaws of UTM securely.
4. Apply tensile load gradually at a uniform rate.
5. Record the load at which yielding starts, indicated by a sharp drop or plateau in the load-deformation graph.
6. The yield strength is calculated using:
Yield Strength (MPa) = Yield Load (N) / {Cross-sectional Area (mm}^2)
Acceptance Criteria:
- As per IS 1786:2008, the yield strength should not be less than:
- Fe415: 415 MPa
- Fe500: 500 MPa
- Fe500D: 500 MPa with higher elongation
- Fe550: 550 MPa
11. Elongation (Ductility) Test of Reinforcement Steel
Objective: To determine the percentage elongation of the bar after fracture, which reflects the ductility of steel — its ability to deform before breaking.
Apparatus Required:
- Universal Testing Machine (UTM)
- Steel specimen with measured gauge length
- Measuring scale or extensometer
Procedure:
1. Take a steel rod of known diameter and mark the original gauge length (Lo) on it.
2. Place the bar in the UTM and pull it under tension till it breaks.
3. After fracture, take both pieces, bring them together, and measure the final gauge length (Lf).
4. Calculate the percentage elongation using the formula:
Elongation (%) = [(L_f – L_o) / (L_o)] * 100
Acceptance Criteria (IS 1786:2008):
- Minimum percentage elongation should be:
- Fe415: ≥ 14.5%
- Fe500: ≥ 12%
- Fe500D: ≥ 16%
- Fe550D: ≥ 14%
- More ductile steel (like Fe500D) is recommended for seismic or dynamic structures.
Usage of Reinforcement Steel in Construction
Reinforcement steel is used in RCC (Reinforced Cement Concrete) structures to provide tensile strength, since concrete alone is strong in compression but weak in tension. Steel gives the flexibility and load-bearing capacity required in structural components like:
- Slabs – for bending resistance.
- Beams – to resist shear and moment.
- Columns – to carry vertical loads.
- Footings & Foundations – to distribute load and resist settlement.
- Retaining Walls – for lateral earth pressure.
- Staircases, Domes, Canopies – where both strength and ductility are needed.
Which Type of Steel Is Better in Different Environments?
1. Normal Environments (Residential/Commercial Buildings):
- Fe 500 or Fe 500D TMT bars are most suitable.
- Offers strength, flexibility, and earthquake resistance.
2. Seismic Zones (Earthquake-Prone Areas):
- Use Fe 500D or Fe 550D.
- These have higher ductility, which helps in energy absorption during tremors.
3. Coastal Areas or Marine Environments:
- Go for Corrosion Resistant Steel (CRS Bars) or Epoxy-Coated Bars.
- These resist rusting due to high salt content in air and water.
4. Industrial Zones with High Chemical Exposure:
- Use Stainless Steel Reinforcement or Galvanized Rebars.
- Better chemical and acid resistance.
5. Bridges and Heavy Infrastructure Projects:
- Fe 600 TMT Bars or Prestressing Steel Wires/Strands.
- High strength with minimal cross-section required.
6. High-Rise Structures:
- Fe 500D or Fe 550D is ideal.
- Reduces congestion in beams and columns with higher load capacity.
Books
- Design of Reinforced Concrete Structures by S. Ramamrutham – Excellent for understanding the behavior and design of steel in RCC.
- Reinforced Concrete Structures by N. Subramanian – A modern book covering design standards, IS codes, detailing, and construction practices.
- Testing of Metals by A.V.K. Suryanarayana – Covers both destructive and non-destructive steel testing methods in detail.
- Materials of Construction by D.N. Ghose – Good for understanding properties and field testing of steel and construction materials.
- Engineering Materials by R.K. Rajput – Includes steel types, manufacturing, mechanical properties, and lab test procedures.
- IS 1786:2008 – Indian Standard for High Strength Deformed Steel Bars – The Bible for reinforcement steel in India. A must-have reference document.
Conclusion
In the world of civil engineering and construction, reinforcement steel plays a vital role in ensuring structural safety, strength, and durability. From the basic definition to understanding its properties, IS code guidelines, and practical calculations, everything revolves around accuracy and proper knowledge.
We explored the different types of reinforcement steel, their physical and mechanical properties, and the standard procedures to test them both in the field and laboratory. While field tests offer quick and essential on-site evaluations, laboratory tests provide a more detailed, scientific understanding of steel quality.
Proper testing and verification of steel before using it in structural elements like beams, columns, slabs, and footings ensures that the building behaves as designed, especially during seismic or high-load conditions. Even minor compromises can lead to catastrophic consequences.
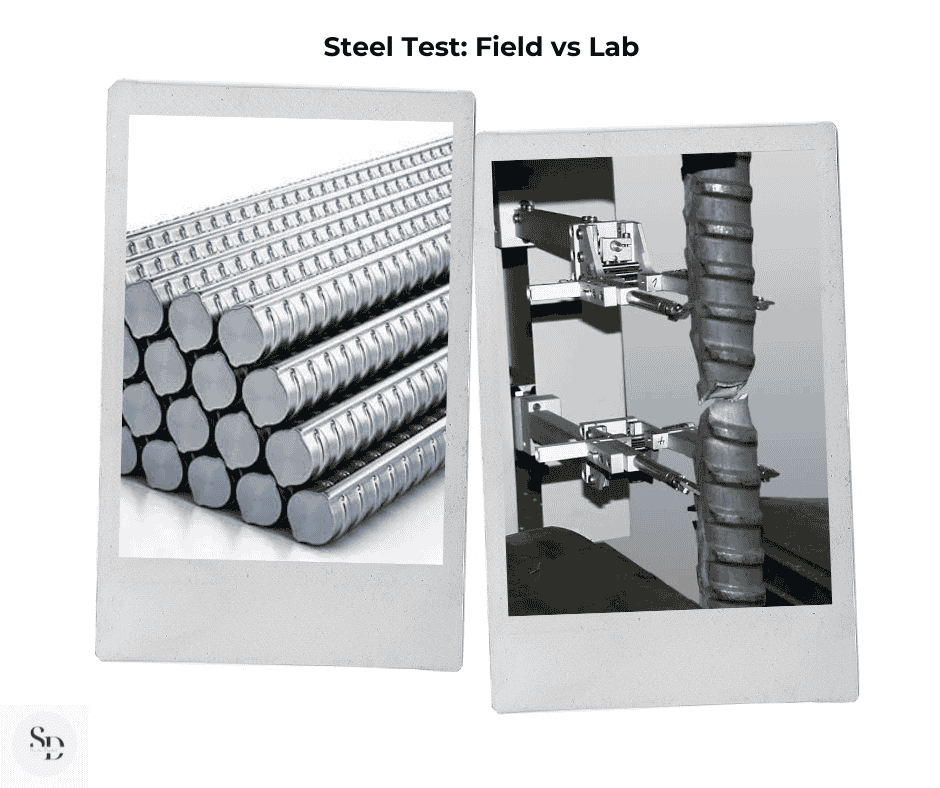
By combining hands-on site knowledge with book-based theory and IS code references, civil engineers and site supervisors can make informed decisions that result in safe, cost-effective, and long-lasting structures.
Thank You Note
Thank you for reading this detailed guide on reinforcement steel and its testing methods. Whether you’re a budding civil engineer, a site supervisor, or a construction enthusiast, we hope this blog helped you understand the significance of testing steel accurately.
Your support encourages us to continue sharing practical knowledge that bridges the gap between textbooks and real-life construction sites.
If you found this guide useful, feel free to share it with others in the construction industry. Stay tuned for more informative content on construction materials and testing methods.
Happy learning and building!
Frequently Asked Questions (FAQs)
Which field test is commonly used to identify reinforcement grade?
What are the essential lab tests for steel reinforcement?
How is corrosion resistance of reinforcement steel checked?
Can TMT bars be welded?
What’s the difference between Fe 415 and Fe 500?
What is the unit weight of steel reinforcement per meter length?
What is the IS code for reinforcement steel in India?
What does Fe415 or Fe500 mean in reinforcement steel?
“Fe” stands for Ferrous, meaning iron-based.
The number 415 or 500 indicates the minimum yield strength of the steel in megapascals (MPa).
So, Fe415 has a minimum yield strength of 415 MPa, and Fe500 has 500 MPa. Higher the number, stronger the steel — but with slightly lower ductility.
What does the ‘D’ mean in Fe500D, Fe550D, etc.?
Compared to normal Fe500, Fe500D has better elongation properties and is more suitable for earthquake-prone or dynamic load areas.
This improved ductility is achieved during the manufacturing process (like controlled quenching in TMT bars) and is tested under standards like IS 1786.
It means the steel can deform more before breaking, which is a safety feature in construction.
Note for Readers
If you’d like to read this blog in your regional language or any other international language, simply click on the Google Translator option located in the bar at the top of the page. This feature allows you to select your preferred language and enjoy the content in a way that’s comfortable for you. We hope this makes your reading experience more enjoyable and accessible!
Disclaimer
This blog is intended for educational purposes only. While we have taken care to include accurate and up-to-date information as per IS codes and field practices, always refer to the latest official IS codes and consult with certified professionals before making engineering decisions on real-world projects.
For more exciting topics, explore our other articles here
One Comment