Brick Test: Field vs Lab – Discover the essential differences between field and laboratory brick testing methods. Learn about their significance, procedures, and which method provides more reliable results for ensuring brick quality in construction.
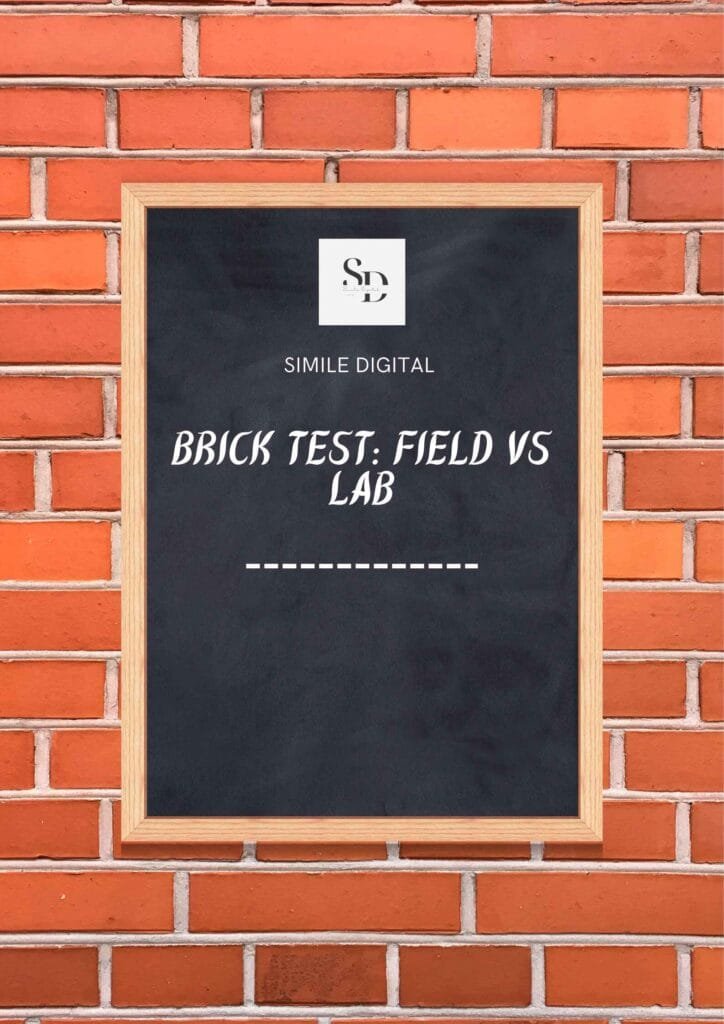
Table of Contents
Introduction
Bricks remain a fundamental building material in construction projects worldwide. From residential homes to large-scale commercial developments, bricks are essential for creating robust and long-lasting structures. However, determining the quality of bricks before use is crucial for construction success.
Quality assurance in brick construction involves two primary testing approaches – Field Tests and Lab Tests. Field testing provides quick, on-site evaluations that can be performed at construction locations, while laboratory testing offers comprehensive, precise analysis using specialized testing equipment and controlled environments.
This comprehensive guide explores both testing methodologies, highlighting their key differences and relative reliability. Whether you’re a construction professional, structural engineer, or someone seeking knowledge about construction materials, this article will help you grasp the significance of brick testing through simple explanations.
What is a Brick?
A brick is a construction element, typically rectangular in shape, manufactured from clay and used extensively in building construction for walls, pavements, and various structural components. This time-tested building material has been used for centuries, valued for its impressive strength and longevity. Bricks acquire their characteristic reddish-brown color through a process of clay molding, air drying, and high-temperature kiln firing.
Density of Brick
Brick density varies based on manufacturing processes and material composition. The typical density range falls between 1600 and 2000 kg/m³.
- Clay bricks: Approximately 1800 kg/m³
- Fly ash bricks: Approximately 1700 kg/m³
- Concrete bricks: Approximately 1900 to 2100 kg/m³
Specific Gravity of Brick
Specific gravity measures a brick’s density relative to water. Most bricks have a specific gravity ranging from 1.8 to 2.5, indicating they’re roughly twice as dense as water.
IS Codes for Bricks
Indian Standard (IS) codes govern brick quality and testing procedures in India. Key IS codes include:
- IS 1077:1992 – Common burnt clay brick specifications
- IS 3495:1992 – Brick testing methods (compressive strength, water absorption, efflorescence, etc.)
- IS 5454:1978 – Brick sampling guidelines
- IS 2212:1991 – Brickwork construction standards
Physical Properties of Brick
Several physical properties determine a brick’s structural integrity, durability, and construction suitability. Essential physical characteristics include:
1.Size and Shape
Bricks must conform to standardized dimensions and maintain consistent rectangular shapes with clearly defined edges.
The standard dimensions of an Indian brick are 190 mm × 90 mm × 90 mm (excluding mortar) and 200 mm × 100 mm × 100 mm (including mortar).
2. Color
High-quality bricks exhibit a consistent red or brown coloration throughout. Bricks with irregular or faded colors often indicate poor burning or inferior quality.
3. Texture
Premium bricks feature a uniform, smooth surface texture free from defects. The presence of surface irregularities, fissures, or cavities typically suggests compromised structural integrity.
4. Density
Brick density typically ranges from 1600 to 1900 kg/m³, varying by brick type. Higher density values generally correlate with enhanced strength and longevity.
5. Hardness
Quality bricks demonstrate significant resistance to surface scratching. A brick’s quality is questionable if it can be easily marked with a fingernail.
6. Compressive Strength
Structural integrity is measured through compression testing. Quality bricks must demonstrate a minimum compressive strength of 3.5 N/mm² under laboratory conditions.
7. Water Absorption
Moisture resistance is crucial for brick durability. Superior bricks limit water absorption to less than 20% of their dry weight after 24-hour water immersion.
8. Efflorescence
Quality bricks minimize salt deposit formation on their surface when exposed to moisture. Minimal or zero efflorescence indicates superior brick quality.
9. Fire Resistance
Bricks demonstrate exceptional heat resistance, maintaining structural integrity at temperatures reaching 1200°C.
10. Soundness
High-quality bricks produce distinct metallic sounds when struck together, indicating proper firing and density.
Brick classifications
1. Based on Quality
- First-Class Bricks – Premium grade featuring uniform dimensions, ideal for superior construction projects.
- Second-Class Bricks – Standard quality with minor irregularities, suitable for general construction.
- Third-Class Bricks – Lower grade, primarily used in temporary structures
- Fourth-Class Bricks – Over-fired bricks utilized mainly as road construction aggregates
2. Based on Material
- Burnt Clay Bricks – Traditional clay-fired construction units
- Fly Ash Bricks – Sustainable alternatives combining fly ash and cement
- Concrete Bricks – Engineered units comprising cement, sand, and aggregates
- Sand-Lime Bricks – High-strength units featuring smooth surface finishing
- Fire Bricks – Specialized heat-resistant units for high-temperature applications
- Engineering Bricks – Highly durable units for foundation and moisture protection
3. Based on Shape and Design
- Perforated Bricks – Engineered units featuring strategically placed holes that reduce overall weight while enhancing ventilation capabilities.
- Bullnose Bricks – Specially designed units with smoothly rounded edges, primarily utilized for corner installations and decorative architectural elements.
- Paving Bricks – Durable units specifically manufactured for external applications including roadways, residential driveways, and pedestrian pathways.
- Capping Bricks – Specialized units designed to provide professional wall termination and enhanced aesthetic appeal.

4. Based on Manufacturing Process
- Hand-Made Bricks – Traditionally crafted units through manual molding techniques followed by kiln firing.
- Machine-Made Bricks – Precision-engineered units produced through automated processes, ensuring dimensional consistency and superior construction quality.
- Sun-Dried Bricks (Unburnt Bricks) – Naturally cured units through solar exposure, primarily utilized in temporary construction applications.
5. Based on Purpose
- Facing Bricks – Premium-quality units specifically designed for exterior wall applications where visual appeal is paramount.
- Fire Bricks – Specialized heat-resistant units engineered for high-temperature applications including furnace and fireplace construction.
- Hollow Bricks – Lightweight construction units featuring internal cavities that provide enhanced insulation properties, commonly used in partition wall systems.
Methods of Brick Manufacturing
Brick manufacturing encompasses various methodologies, determined by resource availability, quality requirements, and production scale objectives. The primary manufacturing approaches include:
1. Hand Molding Method (Traditional Method)
- In this method, bricks are shaped manually using wooden or metal molds.
- Commonly used in small-scale brick production.
- Requires skilled labor but does not need heavy machinery.
There are two types of hand molding:
- Ground Molding: The mold is placed on the ground, and clay is pressed into it.
- Table Molding: Molding is done on a raised platform for better accuracy.
- Advantages: Simple and cost-effective.
- Disadvantages: Labor-intensive, slow production, and uneven brick quality.
2. Machine Molding Method
- Machines are used to press the clay into molds, ensuring uniform size and shape.
- Suitable for large-scale production.
There are two types of machine molding:
- Plastic Molding: Clay is made soft and pressed into molds using machines.
- Dry Press Molding: Clay with very little water is pressed under high pressure in steel molds.
- Advantages: Faster, more uniform bricks, higher strength.
- Disadvantages: High initial investment in machinery.
3. Wire Cut Brick Manufacturing (Extrusion Process)
- A continuous process where clay is extruded through a rectangular opening and cut into bricks using wires.
- Produces highly uniform bricks, widely used in modern brick factories.
- Advantages: Fast production, uniform shape, and smooth texture.
- Disadvantages: Requires advanced machinery and higher energy consumption.
4. Clamp Burning Method
- A traditional method where molded bricks are stacked in a heap (clamp) and fired using coal, wood, or cow dung.
- The fire burns for several days, and bricks are left to cool gradually.
- Used in rural areas for small-scale production.
- Advantages: Low cost, no need for expensive kilns.
- Disadvantages: Uneven burning, lower strength, and environmental pollution.
4. Clamp Burning Method
- Traditional firing technique utilizing stacked brick arrangements with various fuel sources.
- Extended burning duration with gradual cooling requirements.
- Common in rural production environments.
- Advantages: Economical process without specialized kiln requirements.
- Disadvantages: Inconsistent firing patterns leading to quality variations, reduced structural integrity, and significant environmental emissions due to uncontrolled burning processes.
5. Kiln Burning Method
- The kiln burning methodology employs specialized furnace systems designed to maintain precise temperature control throughout the firing process.
- This advanced technique consistently produces premium-quality construction units through regulated thermal exposure.
The process utilizes various specialized kiln configurations:
- Bull’s Trench Kiln (BTK): Predominantly implemented across Indian manufacturing facilities, featuring circular brick arrangements within excavated trenches enabling continuous production cycles. This traditional yet effective system optimizes fuel efficiency while maintaining consistent output quality.
- Hoffman Kiln: Advanced multi-chambered system incorporating sequential firing zones, maximizing thermal efficiency through continuous operation protocols. The specialized design ensures optimal heat distribution and superior product consistency.
- Tunnel Kiln: Contemporary automated system utilizing conveyor mechanisms to transport units through precisely controlled temperature gradients. This modern approach delivers exceptional quality control while minimizing operational variations.
- Advantages: Delivers superior structural integrity with consistent dimensional stability through controlled firing processes.
- Disadvantages: Necessitates substantial capital investment and extensive operational space requirements.
6. Autoclaved Brick Manufacturing (AAC Bricks)
- This innovative methodology specializes in producing Autoclaved Aerated Concrete (AAC) units, engineered for optimal weight reduction and enhanced thermal performance characteristics.
- The manufacturing protocol incorporates precise material proportioning, combining fly ash, cement, lime, and water, followed by specialized high-pressure steam treatment within autoclave chambers.
- Advantages: Produces lightweight construction units featuring superior thermal insulation properties while maintaining optimal energy efficiency ratings.
- Disadvantages: Involves higher production costs and requires specialized manufacturing equipment.
Brick Manufacturing Process
The comprehensive brick manufacturing protocol encompasses multiple sequential stages, including raw material preparation, unit formation, moisture reduction, and thermal processing. This systematic approach ensures the production of durable construction units meeting specified performance requirements.
Steps in Brick Manufacturing
1. Preparation of Clay
The first step is to prepare the clay, which is the main raw material for bricks. This includes:
Excavation: Clay is dug from the ground and collected.
Weathering: The clay is left in the open air for a few weeks to remove impurities and improve plasticity.
Tempering: Water is added to the clay, and it is mixed thoroughly to make it soft and workable. This can be done manually (by feet) or mechanically (by machines).
2. Molding (Shaping the Bricks)
Once the clay is prepared, it is given the required shape. There are three main methods of molding bricks:
(i) Hand Molding
This is the traditional method where workers fill a wooden or metal mold with clay and shape it by hand.
Used for small-scale production.
Two types:
Ground Molding – Clay is placed on the ground and molded.
Table Molding – Molding is done on a table for better accuracy.
(ii) Machine Molding
Machines are used to press the clay into molds.
Faster and more uniform than hand molding.
Suitable for large-scale brick production.
(iii) Extrusion Molding (Wire Cut Bricks)
The clay is forced through a rectangular opening, and a wire cuts it into bricks of uniform size.
Used in modern brick manufacturing plants.
3. Drying
After molding, bricks contain a lot of moisture.
They are left to dry in the sun or in special drying chambers.
This prevents cracking during burning.
Usually takes 7 to 14 days.
4. Burning (Firing in a Kiln)
Burning makes bricks strong and durable. There are two main types of burning methods:
(i) Clamp Burning (Traditional Method)
Bricks are stacked in a heap (clamp) and covered with fuel (wood, coal, or cow dung).
The fire is lit and left to burn for several days.
Cheap method, but quality control is poor.
Used in rural areas or small-scale production.
(ii) Kiln Burning (Modern Method)
Bricks are stacked inside a kiln (a large furnace) and heated at 900°C – 1100°C.
Produces high-quality, durable bricks.
Types of kilns:
Bull’s Trench Kiln (BTK): Common in India, bricks are stacked in a trench, and fire moves through them.
Hoffman Kiln: Continuous process, more efficient, used for large-scale production.
Tunnel Kiln: Modern and fully automatic, provides uniform heating.
5. Cooling and Storage
After burning, bricks are cooled gradually to avoid cracking.
Once cooled, they are sorted based on quality and stored for use in construction.
Brick Test : Field vs. Lab
Field Tests on Bricks
- Visual Inspection Test
- Soundness Test
- Hardness Test
- Drop Test
- Efflorescence Test
- Water Absorption Test (Field Method)
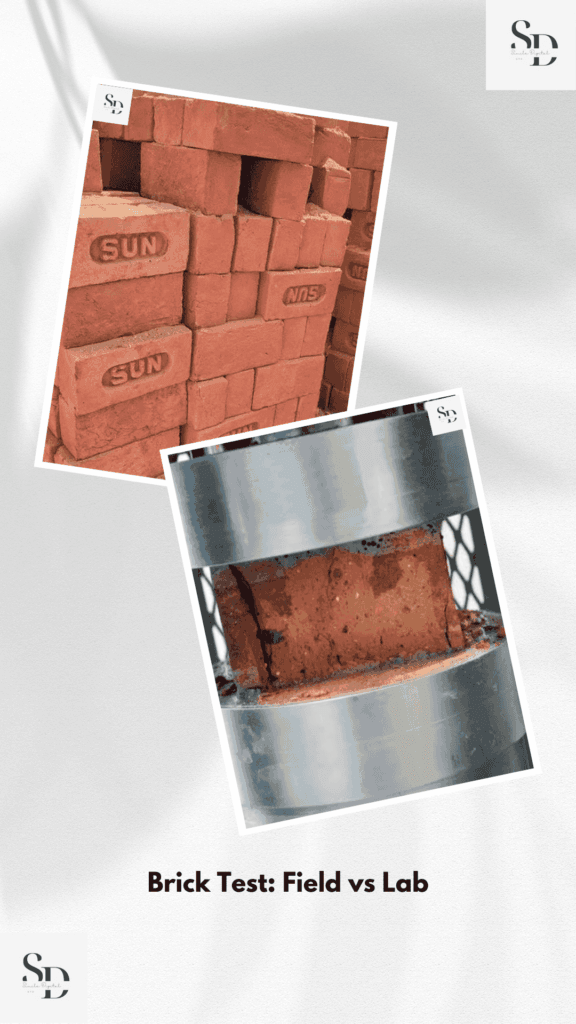
Laboratory Tests on Bricks
- Compressive Strength Test
- Water Absorption Test
- Efflorescence Test
- Modulus of Rupture Test
- Density Test
- Porosity Test
- Heat Conductivity Analysis
- Deformation Analysis
Field Test on Bricks
Field tests provide quick and reliable methods to assess brick quality without specialized laboratory equipment. These practical tests help determine if brick batches meet basic construction standards before proceeding with detailed laboratory analysis.
1. Visual Inspection Test
Purpose: To evaluate the brick’s physical characteristics including shape, size, and color.
Procedure:
- Select random brick samples from the batch.
- Examine the bricks for uniform shape and crisp edges.
- Inspect the surface finish; quality bricks should have an even, smooth texture.
- Look for consistent reddish or copper coloring, which indicates proper firing.
- Discard bricks showing cracks, misshapen edges, or improper burning signs.
Result:
- Quality bricks display clean edges, smooth surfaces, and consistent coloring.
2. Soundness Test
Purpose: To assess brick strength and quality through sound evaluation when struck.
Procedure:
- Select two bricks, holding one in each hand.
- Strike them against each other gently.
- Pay attention to the sound produced.
- Strong, well-burnt bricks produce clear metallic or ringing sounds.
- Weak or defective bricks create dull thuds, indicating potential cracks or poor material.
Result:
- High-quality bricks emit metallic ringing sounds.
- Substandard bricks produce dull sounds and may break easily.
3. Hardness Test
Purpose: To measure the brick surface’s scratch resistance.
Procedure:
- Hold the brick securely.
- Attempt to scratch the surface using a steel nail or sharp knife.
- Check if the scratching creates deep marks or surface damage.
- Strong bricks resist scratching effectively.
- Weak bricks show easy surface damage, making them unsuitable for construction.
Result:
- Quality bricks resist surface scratching.
- Poor bricks show visible damage marks easily.
4. Drop Test
Purpose: To verify the brick’s impact resistance and durability.
Procedure:
- Hold a brick approximately 1 meter (3 feet) above ground level.
- Release it onto a solid surface like concrete or hard flooring.
- Observe the brick’s condition after impact.
- Durable bricks stay intact or break into substantial pieces.
- Weak bricks disintegrate into small fragments or powder.
Result:
- Good bricks maintain integrity or break into large sections.
- Low-quality bricks shatter into tiny pieces.
5. Efflorescence Test
Purpose: To evaluate the presence of soluble salts that may cause unsightly white deposits on brick surfaces over time.
Procedure:
- Select a clean, dry brick and position it on a non-absorbent testing surface.
- Apply water evenly across the brick’s surface and allow it to dry naturally in open air.
- Monitor the brick surface carefully over a 24 to 48-hour period.
- Check for white crystalline deposits appearing on the surface, indicating soluble salt content that could lead to efflorescence (white staining) issues.
- Absence of white deposits suggests the brick is free from problematic salt content.
Result:
- Clean surface without deposits: Indicates high-quality brick material.
- Minor white crystallization: Generally acceptable for construction purposes.
- Significant white deposits: Indicates poor quality, unsuitable for construction use.
6. Water Absorption Test (Field Method)
Purpose: To determine the brick’s water absorption capacity, as excessive absorption can compromise structural integrity.
Procedure:
- Record the initial weight of a completely dry brick (W1) with precision.
- Submerge the brick entirely in clean water for a 24-hour duration.
- Remove the brick and carefully wipe away surface water.
- Measure and record the saturated weight (W2).
- Calculate water absorption percentage using:Water Absorption (%) = [(W2 – W1) / W1] × 100
- Results below 20% indicate suitable quality.
- Absorption exceeding 20% suggests excessive porosity, making the brick unsuitable.
Result:
- Water absorption under 20%: Appropriate for construction use.
- Water absorption over 20%: Indicates structural weakness, avoid using.
7. Dimension Test
Procedure:
- Random Sample Selection: Choose 20 bricks from the available batch.
- Linear Arrangement: Place bricks in a straight line on a level surface without pressure.
- Measurement Process: Record total length, width, and height of all 20 bricks.
- Average Calculation: Divide total measurements by 20 for individual brick dimensions.
- Standard Comparison: Verify measurements against IS 1077 specifications.
Laboratory Tests on Bricks
Laboratory testing ensures comprehensive evaluation of brick strength, water absorption, durability, and overall quality. Below are detailed procedures for main laboratory tests with required equipment.
1. Compressive Strength Test
Purpose: To evaluate maximum load-bearing capacity before failure.
Required Equipment: Compression Testing Machine (CTM), plaster of Paris or cement paste, precision scale, vernier caliper.
Testing Procedure:
- Apply a uniform, thin coating of cement paste on both top and bottom surfaces to ensure even load distribution.
- Position the brick carefully in the center of the Compression Testing Machine platform.
- Gradually increase the pressure at a consistent rate until the brick reaches its breaking point.
- Record the maximum load value at which structural failure occurs.
- Calculate compressive strength using the formula: Maximum Load divided by Surface Area.
Standard Specifications:
- First-class bricks must demonstrate minimum strength of 10 N/mm²
- Second-class bricks should exhibit strength between 7 to 10 N/mm²
- Common building bricks require strength ranging from 3.5 to 7 N/mm²
2. Water Absorption Test
Purpose: To evaluate moisture absorption capacity, which directly impacts brick durability.
Required Equipment: Precision weighing scale, water immersion container, temperature-controlled drying oven.
Testing Procedure:
- Record initial weight of completely dry brick (W1)
- Submerge brick completely in water for 24-hour duration
- Remove and wipe surface moisture carefully
- Measure saturated brick weight (W2)
- Calculate absorption percentage using formula: [(W2 – W1) / W1] × 100
Standard Requirements:
- First-class bricks: Maximum water absorption below 20%
- Second-class bricks: Maximum water absorption below 22%
- Third-class bricks: Maximum water absorption below 25%
3. Efflorescence Test
Purpose: To identify potential salt deposit formation that could compromise brick integrity.
Required Equipment: Shallow testing dish, pure distilled water, measurement tools.
Testing Procedure:
- Place dry brick in dish containing distilled water (2.5 cm depth)
- Maintain 24-hour soaking period for capillary water absorption
- Remove and allow natural drying
- Inspect for white salt formation and repeat if necessary
- Extensive white deposits indicate quality issues
Standard Requirements:
- Quality bricks should show minimal to zero salt deposit formation
4. Modulus of Rupture Test (Bending Test)
Purpose: To assess brick resistance to bending forces.
Required Equipment: Flexural testing apparatus, measurement tools.
Testing Procedure:
- Position brick on support points
- Apply centered load gradually
- Increase force until structural failure
- Document maximum load at failure point
Standard Requirements:
- High-quality bricks must demonstrate substantial bending resistance
5. Density Test
Purpose: To determine brick density for load-bearing evaluation.
Required Equipment: Precision scale, measurement tools, water displacement vessel.
Testing Procedure:
- Measure dry brick weight (W1)
- Calculate volume (V) using length, width, height measurements
- Calculate density using the formula: Density = W1 / V (expressed in kg/m³).
Standard Values:
- Premium quality bricks: 1800 – 2000 kg/m³
- Standard clay bricks: 1600 – 1900 kg/m³
6. Porosity Test
Purpose: This evaluation determines the void spaces (porosity) within a brick, which influences its water absorption characteristics and overall structural integrity.
Required Equipment: Water container, precision weighing apparatus.
Testing Procedure:
- Record the initial dry brick mass (W1)
- Submerge completely in water for 24-hour duration
- Measure the saturated brick mass (W2)
- Calculate porosity percentage using: [(W2 – W1) / W1] × 100
Standard Requirements:
Quality bricks should maintain porosity levels between 12% and 20%
7. Heat Conductivity Analysis
Purpose: This assessment evaluates brick thermal conductivity, crucial for building energy efficiency.
Required Equipment: Thermal conductivity analyzer, heat flow measurement device.
Testing Procedure:
- Position brick specimen in thermal testing apparatus
- Generate heat differential across brick surfaces
- Measure heat transfer rate in W/mK (Watts per meter Kelvin)
Standard Parameters:
- Traditional clay bricks: 0.6 – 1.0 W/mK (thermal insulation properties)
- Fly ash brick variants: 0.3 – 0.8 W/mK (enhanced insulation)
8. Deformation Analysis
Purpose: This evaluation measures brick dimensional stability under sustained loading conditions.
Required Equipment: Specialized loading framework, precision measurement gauge.
Testing Procedure:
- Subject brick to controlled progressive loading
- Maintain constant pressure over extended duration
- Monitor dimensional changes using precision instruments
Standard Requirements:
Quality bricks should exhibit minimal dimensional changes under sustained loading.
Brick Chemical Composition Analysis
The fundamental composition of bricks includes silica, alumina, lime, iron oxide, and magnesia. These components determine crucial properties including strength, longevity, and weather resistance.
1. Silica (SiO₂) – 50-60%
- Provides strength and hardness to bricks.
- Prevents cracking and warping during drying.
- Excess silica makes bricks brittle.
2. Alumina (Al₂O₃) – 20-30%
- Gives plasticity to the clay, making it easy to shape.
- Too much alumina can cause bricks to shrink and crack.
3. Lime (CaO) – 5-10%
- Helps in binding particles together, increasing strength.
- If in excess, it causes cracks and disintegration in bricks.
4. Iron Oxide (Fe₂O₃) – 5-6%
- Provides red or brownish color to the bricks.
- Increases strength and durability.
- Excess iron oxide makes bricks too dark and brittle.
5. Magnesia (MgO) – 1-2%
- Improves resistance to cracks.
- If excessive, it makes bricks weak.
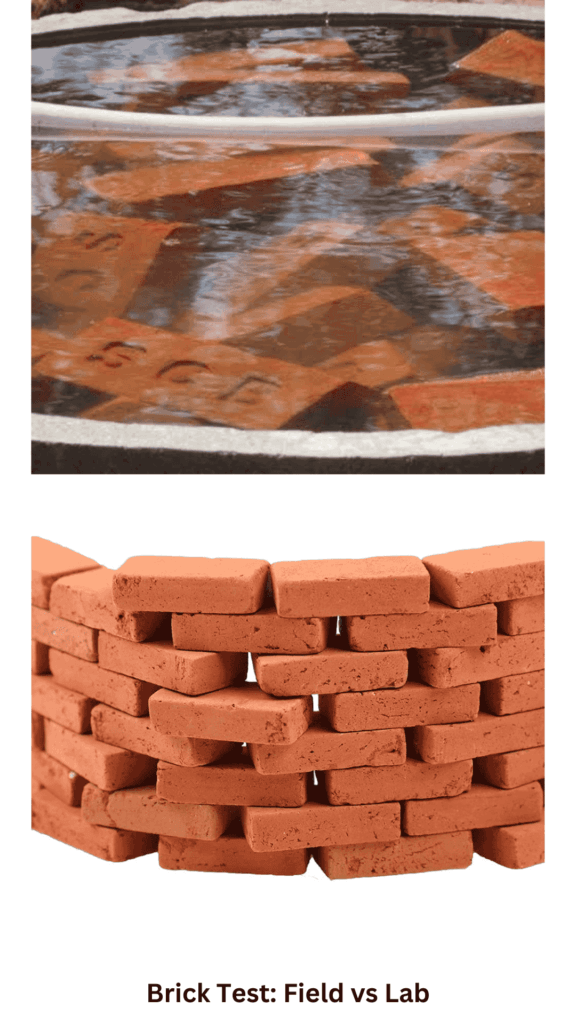
Which Brick Should You Use?
For environmentally conscious construction projects, Fly Ash Bricks or AAC Blocks represent optimal choices. These alternatives deliver exceptional strength, durability, and energy efficiency while minimizing environmental impact.
Consider avoiding traditional burnt clay bricks when possible, as they contribute to soil depletion, increased carbon emissions, and environmental pollution. Instead, prioritize modern, sustainable brick alternatives that align with green building principles and environmental preservation.
Books
1. Brick and Reinforced Brick Structures by P. Dayaratnam and P. Sarah
2. Handbook of Masonry Design and Construction – First Revision by H. C. Visvesvaraya
3. Building Materials and Construction by Anil Kumar Mishra
4. IS 2212:1991 – Code of Practice for Brickworks
5. SP 20:1991 – Handbook on Masonry Design and Construction
Conclusion
Bricks remain fundamental construction materials, offering exceptional strength, durability, and weather resistance across various applications. Quality assurance involves comprehensive field and laboratory testing procedures.
Field testing enables rapid on-site evaluation, while laboratory analysis provides detailed data regarding compressive strength, water absorption, efflorescence, rupture modulus, density, porosity, thermal conductivity, and creep resistance. IS codes establish standardized testing and quality control guidelines.
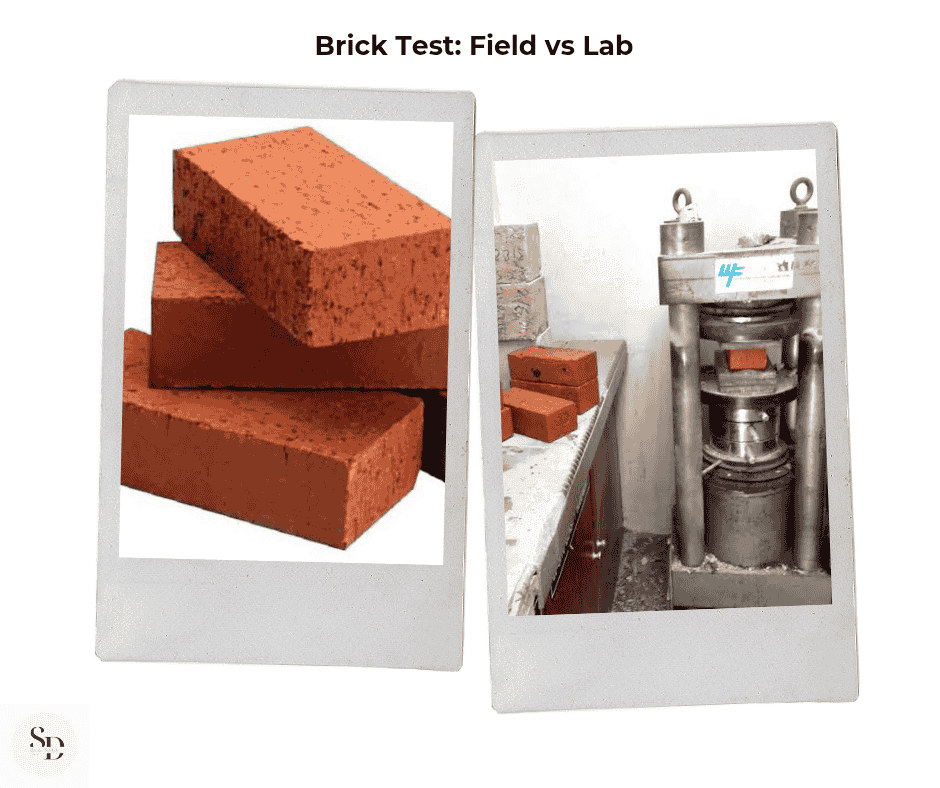
Understanding these testing protocols remains crucial for construction professionals in selecting appropriate brick materials. Quality brick selection ensures enhanced structural integrity and longevity.
Thank You Note
We appreciate your time reviewing this comprehensive guide on Brick Testing – Field vs Lab. This resource aims to provide valuable information regarding brick varieties, properties, manufacturing processes, and testing methodologies. For construction professionals, ensuring compliance with brick quality standards remains essential for structural integrity and durability.
If you found this guide useful, feel free to share it with others in the construction industry. Stay tuned for more informative content on construction materials and testing methods.
Happy learning and building!
Frequently Asked Questions (FAQs)
What are the different types of tests conducted on bricks?
Field Tests: Color Test, Hardness Test, Soundness Test, Drop Test.
Laboratory Tests: Compressive Strength Test, Water Absorption Test, Efflorescence Test, Modulus of Rupture Test, Density Test, Porosity Test, Thermal Conductivity Test.
Why is testing of bricks important?
What are the methods of brick manufacturing?
Machine Moulding: Bricks are manufactured using machines for large-scale production.
What are the different types of bricks?
Based on Composition: Clay bricks, Fly ash bricks, Concrete bricks, Sand-lime bricks.
Based on Quality: First-class, Second-class, Third-class bricks.
Special Bricks: Fire bricks, Engineering bricks, Hollow bricks, Perforated bricks.
What is the specific gravity of a brick?
What is the density of a brick?
First-class bricks: 1800 – 2000 kg/m³
Common burnt clay bricks: 1600 – 1900 kg/m³
Fly ash bricks: 1700 – 1850 kg/m³
What is the IS code for bricks?
Note for Readers
If you’d like to read this blog in your regional language or any other international language, simply click on the Google Translator option located in the bar at the top of the page. This feature allows you to select your preferred language and enjoy the content in a way that’s comfortable for you. We hope this makes your reading experience more enjoyable and accessible!
Disclaimer
This article is for informational purposes only. The data and standards mentioned (such as IS 1077:1992) are based on Indian Standards and may vary based on region and updates in regulations. Always refer to the latest IS codes and consult a professional for precise testing and construction practices.
For more exciting topics, explore our other articles here
Coarse Aggregate Test: Field vs. Lab
5 Comments